Downstream Processing
- Harvesting, purification, and final processing of fermentation products in suitable dosage form for their intended use after completion of fermentation are called downstream processing. Stages of product recovery from fermentation broth are shown in Fig. 1.
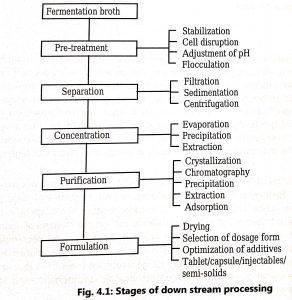
- The downstream process involves three major stages i.e. separation of cells from the fermentation broth, isolation of impure product, and purification and final processing of the product.
- The product formed by fermentation can be intra-cellular or extra-cellular and heat-stable or sensitive. Hence, the downstream process is designed by considering many factors to achieve pure isolated products with the least cost.
- The selection of specific processes depends on the following factors.
- Product location extra-cellular/intra-cellular.
- Product sensitivity.
- The concentration of product or possible yield.
- Properties and use of the product.
- Acceptable standards of purity.
- Possible impurities.
- The economy of process and market price of the product.
Pre-treatment:
- Fermentation broth contains microbial cells, cell fragments, soluble and insoluble medium components along with the active product.
- Pre-treatment is given to fermentation broth to change the viscosity of the medium, biomass size, and interaction between particles.
- Synthetic polymers, cellulosic polycations, and inorganic salts are added into the broth as a flocculating agent.
- These agents can lead to the agglomeration of individual cell particles into Jarge flocs, facilitating separation by centrifugation.
- When a product is intra-cellular, some methods are used to disintegrate the cell to release the intracellular product.
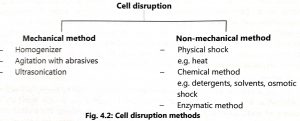
Separation:
- The cells after cell disruption for intra-cellular products and without cell disruption for extra-cellular products are separated by centrifugation or filtration.
- Filtration retains large particles as a cake and allows the passage of liquid through the filter. The flow of liquid through the filter medium is dependent on the area of the filter, the pore size of the filter, and flow resistances by the cake formed on the filter medium.
- Cellulose, glass, ceramics, synthetic membranes, synthetic fibers, cloth, metal, etc. are used as filter media.
- When filtration is not a satisfactory method to remove micro-organisms, centrifugation can be employed. Different types of centrifuges are available with varying r.p.m.
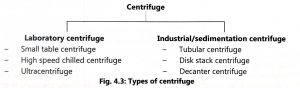
Concentration:
- After the separation of microbial cells, the broth is fractionated or extracted by using different techniques of extraction, evaporation, and precipitation.
- Evaporation is a simple but energy-consuming process mainly for the removal of water. Falling film evaporators, forced film evaporators, plate evaporators, and centrifugal forced film evaporators are commonly used for the concentration of solvents.
- In the product recovery process, precipitation is carried out to enrich and concentrate the product in one step.
- The precipitation technique is commonly used for the recovery of products as well as to separate the impurities. Precipitation is achieved by external agents such as acids and bases (to change the pH); organic solvents like chilled acetone, ethanol, methanol (to change in dielectric properties); salts like ammonium or sodium sulfate (recovery of proteins), non-ionic polymers like polyethylene glycol (PEG), polyelectrolytes and protein binding dyes.
- Extraction is commonly applied in a large-scale fermentation for concentration and purification. Solubility and polarity of the product play a major role in the selection of solvent for extraction.
- Multistage extraction or counter-current extraction is also employed with a high extraction yield. Mixer settlers, column, and centrifugal extractors are commonly used for the extraction, Solvents used for extraction are expensive. Hence, all solvents are recovered and re-circulated in the extraction process.
Purification:
- The crude product obtained by concentration is then purified by fractional precipitation, crystallization, and chromatographical techniques.
- Crystallization is used especially in the recovery of acids, solvents, and in the purification of various compounds. The crystals obtained by crystallization are separated by filtration, redissolved in a suitable solvent, and then re-crystallized to assure the removal of all impurities.
- Chromatographic techniques are commonly used in the isolation and purification of fermentation products.
- The components are distributed between a stationary phase and a mobile phase. The stationary phase is a packed column of uniformly sized particles equilibrated with a suitable solvent, while the mobile phase is a solvent that moves in this packed column (Fig. 4).
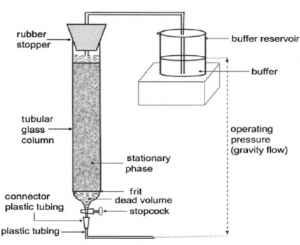
- The mixture to be separated is packed into a column followed by mobile phase. Adsorption chromatography, ion-exchange chromatography, gel-filtration chromatography, affinity chromatography, reverse phase chromatography, and high-performance liquid chromatography are the commonly used techniques for the purification of proteins and pharmaceuticals. The purity of products is continuously confirmed by paper and thin-layer chromatography.
- Different types of paper chromatography are used for checking the purity of isolated products such as ascending paper chromatography, descending paper chromatography, and circular paper chromatography.
Formulation:
- Antibiotics, proteins, and enzymes are formulated as a solution, suspension, or as dry powders. Stabilizers such as ammonium sulfate salt, sorbitol, glycerol, PEG, etc. are added to these preparations.
- Depending on dosage form, different other additives are also added in the final formulation e.g. diluents, lubricating agent, suspending agent, emulsifying agent, coloring agent, etc.
- Drying is the most essential step mainly for protein products. Contact dryers (e.g. drum dryer), convection dryers (e.g. spray dryer, fluidized dryer), and radiation dryers (freeze dryer) are commonly used for drying the final product.
- The antibiotics are packed in sterile vials as a powder or suspension for parenteral or oral use. They may be formulated as film-coated tablets.
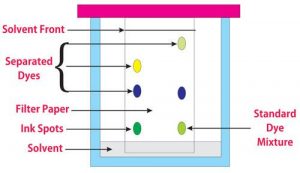
- Estimation of the fermentation products is necessary during drying in downstream processing and at the end of the process. Gravimetry, spectrophotometry, specific gravity, optical density, packed cell volume, total viable count, measurements of cell components, Counting chambers, and chromatography are the common methods used for the estimation of fermentation products.
- Quality control of fermentation products is done during the process and the finished final product. During downstream processing, the efficiency of the unit operations is determined by product evaluation at each step.
- Quality assurance or quality control tests for fermentation products include sterility testing, pyrogen testing, toxicity testing, allergy testing, microbiological assays, and carcinogenicity testing. It must satisfy all government standards before being marketed.